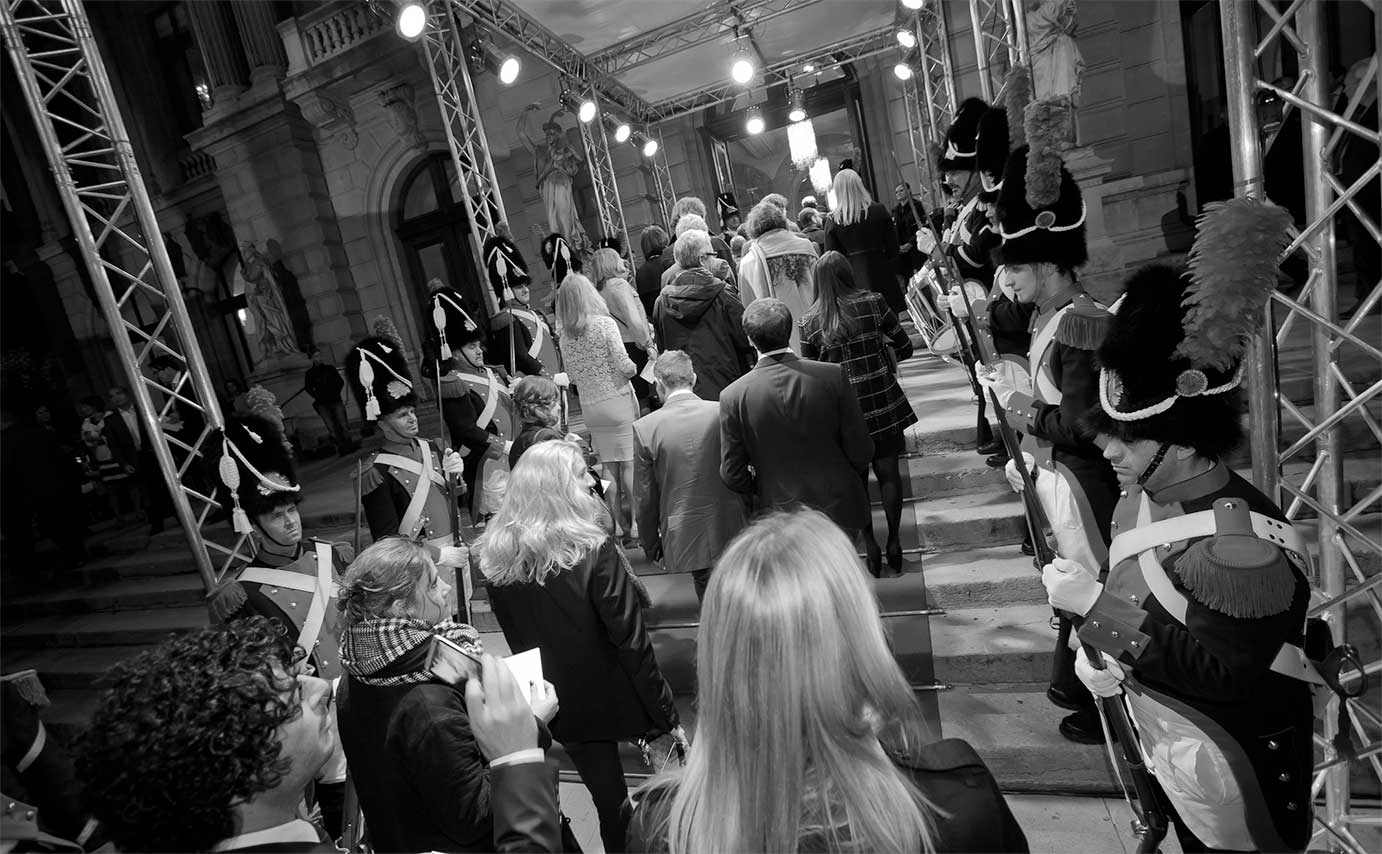
Dual Time Resonance Sapphire
Power reserve: 110 h, 25200 vph
Poinçon de Genève
Skeleton movement
Resonance movement
Dual Time Resonance Sapphire : crystal-clear evolution
With the introduction of the Mirrored Force Resonance, Armin Strom revolutionized both the practical and aesthetical benefits of using the physical properties of resonance in wristwatches. The Mirrored Force Resonance demystified resonance by placing two oscillators resonating through the patented Resonant Clutch Spring front and center. Here, the dials and dual regulators sit on top of two vertically-stacked, independent movements.
To highlight the highest level of horology and micro-engineering, Dual Time Resonance highlights the duality of the two independent resonating movements by replacing the vertical ‘stacked’ movement architecture with horizontal side-by-side movements. This has the added attraction of enabling appreciation of even more of the impeccably finished movement.
Armin Strom technical director Claude Greisler explains, “Developing a perpetual calendar or tourbillon would have been far easier than the years we spent calculating and validating the Resonance Clutch Spring; it was uncharted territory.”
Dual Time Resonance Sapphire now removes any and all barriers to appreciation: the case ‘disappears’ in an unabashed celebration of the reliably resonating calibre ARF17 movement seemingly floating between strap ends. The transparent case of Dual Time Resonance largely disappears from view, which amplifies the form-follows-function horizontal movement architecture of the caliber ARF17.
“The transparency of the case goes in line with the work we are doing in the Switzerland-based manufacture. We show what we make ourselves and we are driven by perfection” says Armin Strom founder Serge Michel. “There is a lot of work done by hand and we wanted to have the possibility to show the 360° decoration on every piece from Armin Strom and this one in particular.”
Dual Time Resonance Sapphire : sapphire crystal
The attraction of sapphire crystal watch cases is (transparently) obvious; the difficulty, though, in cutting, milling, polishing, and assembling sapphire crystal case components is extreme, especially in relatively large — in this case 59 mm long — case components.
Sapphire crystal rates 9.0 on the Mohs scale, as opposed to 9.5 for moissanite and 10 for diamond. Diamond-coated tools spend days cutting, then milling the case components from massive sapphire crystal blocks.
These are then left for a few days to allow any tension generated by the heat of machining to be evenly distributed throughout the crystal. The case is then polished for days, transforming the opaque milled crystal into one that is crystal clear.
Sapphire crystal’s main challenge is its extreme hardness. Like the less glamorous but equally contemporary ceramic cases, hardness is the cause of susceptibility to chipping, cracking, or shattering: sapphire crystal is fragile, and this creates a manufacturing process that is very long,and very complicated with a lot of breakage.
Dual Time Resonance : inspiration and development
Masterpiece 1 Dual Time Resonance was developed as a showcase for Armin Strom’s technical and artistic excellence, bringing the phenomenon of resonance front and centre.
The Resonance Clutch Spring allows the mysterious force of resonance to be visualized in real time. It’s a visually entertaining complication as well as a technical tour de force, a performance-enhancing mechanism so obvious that you can see it.
While it has been long known that resonance in watch and clock movements with synchronized coupled oscillators improves accuracy by averaging slight differences in the precision of each movement – and in wristwatches minimises adverse effects of shocks on precision – it is less known that resonance also conserves vibrational energy normally lost through supporting the regulator.
Armin Strom’s laboratory testing has revealed gains in precision of 15-20% for two COSC-certified chronometer-level regulated movements placed in resonance.
But the manufacture did not set out to make a dual time watch; the principal aim was to showcase the resonance movement to the maximum. The movement architecture was a perfect meld of form and function: spreading the two movements apart horizontally in the Dual Time Resonance – compared to the two vertically stacked movements of the Armin Strom Mirrored Force Resonance – meant that a dial on each movement was a logical choice.
And with two time displays, dual time follows naturally. The independent second time display can also function as a countdown indicator or for tracking elapsed time. Two independent movements mean two independent time displays, one 24-hour indicator, four mainspring barrels, and two conical power reserve indicators.
In the pursuit of horological accuracy, precision, and rate stability, resonance has usually involved using two connected independent movements to allow fine tuning of the distance between them. Until Armin Strom, precise adjustment of the distance between the two regulators has been necessary to incite resonance. However, the Armin Strom Resonance Clutch Spring eliminates the necessity for fine tuning the distance, ensuring a much more reliable and efficient resonant system only needing up to 10 minutes to synchronise. The idea of resonance has endured for three centuries for a reason, but that doesn’t mean you can’t improve upon it.
Armin Strom’s patented Resonance Clutch Spring is an innovative way of upgrading an old concept, one that is horology’s very reason for being: precision and accuracy.
The CSEM (Centre Suisse d'Electronique et de Microtechnique) has officially certified Armin Strom’s resonance system based on the Resonance Clutch Spring as being a true system in resonance.
What is resonance?
Any body in motion causes vibrations in its surroundings. When another body with a similar natural resonant frequency to the first receives these vibrations, it absorbs energy from it and starts vibrating at the same frequency in a sympathetic manner. For example, a trained singer can hold a note causing a tuning fork tuned to the same frequency to vibrate.
For the oscillators of a watch movement to be able to synchronize with each other, they have to be closely tuned. Imagine a small child trying to synchronize steps with an adult: he or she is unlikely to synchronise for more than a few steps as the systems are too dissimilar to resonate.
Or imagine yourself pushing a child on a swing: the child and the swing make a natural pendulum, which will have an inherent natural frequency (speed of swing back and forth). If you push at the wrong frequency (too fast or too slow) then you are likely to block the motion and slow the swing down; however, if you push at or near the natural frequency of the swing then you will increase the amplitude (distance the swing moves) of the child/swing system.
In horology, the phenomenon of synchronized motion has fascinated watchmakers since the time of Christiaan Huygens (1629-1695). Huygens, inventor of the pendulum clock, was the first to discover the resonance of two separate pendulum clocks, which he logically surmised should keep slightly different time. When hung from a common beam, however, the pendulums of the adjacent clocks synchronized; subsequent researchers confirmed that the common wooden beam coupled the vibrations and created resonance. The two pendulums functioned as one in a synchronous manner. In the eighteenth century, Abraham-Louis Breguet demonstrated his mastery of the physics with a double pendulum resonance clock.
An outside shock slowing down one of them increases the speed of the other one by the same amount; but both will strive to get back in resonance, averaging and minimizing the effects of the outside influence as they find their rhythm. What was true for Huygens’ and Breguet’s clocks is just as true for Armin Strom’s wristwatch.
The advantages of resonance are threefold: 1) stabilizing effect on timekeeping, meaning better accuracy; 2) conservation of energy (think of a professional cyclist riding in the shadow of another cyclist in a racing situation); and 3) reduction of negative effects on timekeeping accuracy due to outside perturbation such as shock to the balance staff, which in turn keeps the rate stabler (better accuracy).
While the advantages of resonance have been known for centuries, only a handful of clockmakers and watchmakers have created timepieces deliberately and successfully exploiting the phenomenon of resonance, including Antide Janvier (1751-1855) and Abraham-Louis Breguet (1747-1823).
Armin Strom today : Serge Michel and Claude Greisler in partnership
Children born in the same year growing up in a town like Burgdorf (population 15,000) are likely to know each other, either through school, family, or mutual friends. Such is the case with Serge Michel and Claude Greisler, who grew up in the town where Armin Strom, famous for his watch skeletonisation skills, had his watch shop and workshop. When the plastic Swatch watch was launched, having been developed and produced in the nearby city of Bienne, Serge was hooked and started collecting Swatches, following in the footsteps of his father, who is also a watch collector. It was a passion that would continue throughout his life.
But while Serge went on to study marketing, Claude decided to become a watchmaker, first attending the watchmaking school in Solothurn before specializing in the restoration of vintage and complicated movements at the CIFOM technical school in Le Locle, concluding his studies there with a specialization in movement development.
Both Serge and Claude had known about watchmaker Armin Strom from a very young age. Serge not only remembers peering through the window of his store to look at the watches, but also the fact that Armin Strom was a local celebrity known for travelling far and wide to deliver his watches to customers. Claude had also known about Armin Strom from an early age, since his parents owned an optician’s shop right next to Armin Strom’s store in the historic centre of Burgdorf. In Serge’s case, Armin Strom became a family friend and at convivial dinners the talk would often turn to watches and watchmaking. It was hardly surprising, therefore, that the family friendship evolved into a business relationship in 2006 as Armin Strom was considering how to ensure the future of his name and reputation.
“I was convinced that this is a fantastic opportunity to maintain this tradition of skeletonizing watches and develop it for the future, and my family agreed,” says Serge. “That was back in 2006, but at the time we didn’t really have the knowledge about watchmaking. We had the passion, but we needed someone who was an expert on the watchmaking side of things, which is where Claude comes in. He joined me in 2007, and we started to set up the brand Armin Strom and change the direction from purely handmade skeletonised watches to a fully equipped manufacture, which we are today.”
For Claude Greisler, it was like a dream come true. “When Serge first called me and talked about taking the brand to the next level with a factory and taking the brand over from someone from the same town as us, it was the perfect mix. Armin Strom had always been interested in the mechanics of the movement, so to be able to take this philosophy forward was a fantastic opportunity.”
The core element in the vision of the duo was always to consider the movement as the very heart of the watch, which meant that the company would need to be a manufacture to produce its own movements. “This was not just a question of designing our own movements,” explains Claude, “but being able to take exactly the kind of brass that we wanted and the type of steel that we wanted to make the best possible plates, bridges, screws and pinions that we could and to do the electroplating and finishing, as well as the assembly, all in-house.”
Armin Strom : A fully integrated manufacture
While Armin Strom is a vertically integrated complete horological manufacture, no new watch movement would ever have seen the light of day were it not for Claude Greisler, who puts ideas such as the one for the revolutionary Mirrored Force Resonance movement down on paper before they are transferred to computer-aided design programmes to start modelling the movement. Like so many things at Armin Strom, all of this is done in-house, with the dimensions calculated down to a precision of one micron to provide the inputs for the machines that will eventually produce the smallest of components.
At Armin Strom, the majority of components in the movement, with the exception of the escapement and balance spring, are produced in-house. Small round components like screws, pinions and gear wheels are produced by profile-turning machines, which gradually whittle away long steel or brass rods from the side to cut teeth or axles. Larger components such as base plates and bridges are produced from brass on CNC machines, which are capable of machining along multiple axes consecutively using different tools for different operations, moving the component using robotic arms.
Particularly small and delicate components, such as smaller bridges, levers and springs, are produced using wire erosion. This involves threading a wire that is not much smaller than a human hair through a tiny hole in the metal. An electrical current running through the wire reacts with a solution in which the entire working plate is dipped, thus “eroding” minuscule amounts of the metal. This allows particularly delicate operations to be carried out while maintaining the structural integrity of the metal. In fact, Armin Strom does not produce any of its components by stamping because of the stresses that this places on the metal.
Once the raw components are manufactured, they are engraved, bevelled, polished and decorated with circular graining or Geneva stripes by hand before moving to the in-house electro-plating department. Here, all steel and brass components are first given a gold plating before a layer of nickel is added to prevent corrosion and harden the surface. After cleaning, the parts are then dipped in other electroplating baths to give them their final colour such as rhodium, ruthenium or rose gold. It is only thanks to its mastery of electroplating techniques inside its own workshops that Armin Strom can allow customers to choose preferred colours for the coating on different components.
Only then can the individual components of the movement be passed on to the watchmaker for assembly. After setting the jewels into the base plate and bridges, the watchmaker adds the gear train and mainspring.
After the escapement and balance wheel are positioned, the movement finally comes to life…only to be completely disassembled, cleaned and dried before being re-assembled and lubricated. After several days of testing the precision, the watch is finally ready.